Определение величины припусков на обработку вала. Определение промежуточных припусков, допусков и размеров
При выполнении ломавшего задания расчет припусков на механическую обработку для заданных операций производятся статистическим (табличным) методом, используя нормативные материалы, приведенные в/З.,.5, 8, 9, 10. И, 14...18, 21,29/.
Расчет межоперационных припусков и предельных размерах обрабатываемых поверхностей по технологическим переходам (операциям) ведется в определенной последовательности;
1.Анализ исходных данных. Исходными данными для расчета припусков являются: принятый метод получения заготовки (прокат, штамповка, литье под давлением, литье машинной формовкой и т.д.); принятый технологический процесс обработки; приняли станок, приспособления и режущие инструменты.
При анализе по чертежу детали уясняют форму, размеры, точность и параметры шероховатости обрабатываемых поверхностей детали. Уточняют базовые опорные поверхности, способ установки и закрепления на станке заготовки, последовательность (маршрут), обработки заданной поверхности на заготовке, с учетом точности (квалитета) и параметра шероховатости, достигаемых после каждого этапа обработки.
2. Определение, межоперационных припусков. Расчет начинают с последней (финишной) операции обработки. Из нормативных таблиц, приведенных в /3...5,8,9,11,14,18,21,26/, находят величину припуска на каждую операцию и затем рассчитывают операционные размеры заготовки.
В ряде источников отсутствуют сведения о величине операционного припуска Z1 или 2Z1 на первый (предварительный, черновой) технологический переход. В этом случае величину его можно определить расчетом.
При обработке плоской поверхности промежуточный припуск на сторону на первый черновой переход Z1 определяют по формуле:
Z1=Z0-(Z2+Z3+…+Zn);
при обработке поверхностей вращения тел операционный припуск на диаметр на первый черновой переход 2Z1 находят по формуле:
Z1=Zod-(2Z2+2Z3+…+2Zn),
Где Z2, Z3,…Zn припуски на последующие технологические переходы.
3. Расчет межоперационных номинальных размеров.
Исходной величиной для расчета межоперационных размеров при обработке заданной поверхности является размер этой поверхности по рабочему чертежу детали с указанием поля допуска и параметра шероховатости. За исходный расчетный размер принимают при обработке наружных поверхностей вращения наибольший предельный размер, а при обработке отверстий - наименьший предельный размер.
Межоперационные номинальные размеры при обработке наружных поверхностей определяют путем последовательного прибавления к исходному расчетному размеру рассматриваемой поверхности межоперационных припусков в порядке обратном ходу технологического процесса обработки этой операции.
Для наружной поверхности межоперационные размеры рассчитывают во формулам dз=dн+2Zy ; d2=dз+2Z3; d1=d2+2Z2; и для проверки расчета определяет диаметр заготовки dз=d1+2Z1. При обработке внутренней поверхности межоперационные размеры определяют путем последовательного вычитания неисходного расчетного размера готового отверстия промежуточных припусков в порядке, обратном ходу технологического процесса обработки отверстия.
Для внутренних поверхностей межоперационные размеры определяют по формулам: Dз=Dн-2Z; D2=Dз-2Z3; D1=D2-2Z2 и для проверки расчета определяют диаметр отверстия в заготовке Dз=D-2Z1.К каждому межоперационному размеру записывают поле допускаемого отклонения с указанием квалитета и числовое значение допуска, а также параметр шероховатости, которые установлены ранее. При этом межоперационные размеры округляют в сторону увеличения припуска до того же знака, что и допуск размера. Для наружных поверхностей межоперационные размеры выполняются с полем допуска с основным отклонением h, а для внутренних поверхностей с полем допуска с основным отклонением Н соответствующих квалитетов.
Пример 5. Определить по нормативным таблицам припуски на обработку и рассчитать промежуточные предельные размеры для шейки вала диаметрам Ø40h6 (0,016) и длиной 35 – 0,34 мм с шероховатостью поверхности Rа= 1,25 мкм.
Общая длина детали по чертежу 250 - 0,94. Материал детали сталь 45 (40…45 НRCэ) Заготовка - прокат. Масса -6,29 кг.
Решение1. Составление маршрута обработки шейки вала Ø40h6. Поскольку шейка обрабатывается с точностью по 6-му квалитету и шероховатостью Rа=1,25 мкм, технологический маршрут состоит из предварительного точения, чистового точения. однократного шлифования (прил.9 метод, указаний или /3, табл.3.1, с.40/, /Т8, табл.5, с.161/).
2. Определение припусков, допусков и предельных размеров обрабатываемой поверхности по технологическим переходам.
Для компактности, наглядности и сокращения текстовой части пояснительном записки студенту рекомендуется составить карту, расчета (табл. 5) и занести в нее найденные данные.
Таблица 5
Расчет припусков, допусков и предельных размеров по технологическим переходам на обработку поверхности Ø40- 0,16 вала – статистический метод расчета (пример заполнения)
Маршрут обработки |
Наименьшее значение припуска 2Zimin, мм |
Расчетный размер |
Допуск, мм |
Предельные размеры, мм |
Предельные значения припусков |
||
Наибольший |
Наименьший | ||||||
Наружная поверхность шейки вала диаметром 40h6 (-0,016), с шероховатостью поверхности Ra=1,25мкм Заготовка |
Принимаем | ||||||
Точение: черновое | |||||||
чистовое | |||||||
Шлифование |
Общие припуски 7,734 6,6
При заполнении отдельных граф необходимо руководствоваться следующими рекомендациями.
Графа I. Заполняется, пользуясь технологическим процессом дм каждой обрабатываемой поверхности по всем операциям и переходам, начиная о заготовки до последней операции (перехода),
Графа 2. Значение наименьшего припуска определяют из справочников (например, / 5, табл.3.14, с.41/, /8,табл.10,2, о,132/ и др.) для каждого технологического перехода (операции). Если рассчитывают припуски на цилиндрические поверхности, то рекомендуется в этой графе указывать припуск на диаметр (2Zimin).
Графа 3. В эту графу заносят сначала размеры детали для конечного перехода, наименьший предельный размер по чертежу для обработки отверстий или другой внутренней поверхности. Припуск на черновую обработку получают вычитанием наименьшего размера черновой обработки, полученного по расчету, из наименьшего размера заготовки, полученного по ГОСТ 1855-55* и ГОСТ 2009-55* для отливок, по ГОСТ 7062-67*, ГОСТ 7505-55* и ГОСТ 7829-70х для поковок и штамповок. Размеры отдельных видов заготовок по ГОСТ приведены также в / 3/,/5/, /18/, а также в прил.5 метод. указаний. Окончательный размер заготовки из прутка или трубы выбирают по сортаменту. Наименьший размер прутка по сортаменту должен быть больше или равен расчетному размеру.
Графа 4. Допуск на окончательный размер должен быть равный допуску на размер детали по чертежу).
Допуски на операционные размеры не долями превышать экономической точности обработки на данной операции. Как правило, каждая последующая обработка увеличивает точность на1...2 квалитета.
Основанием для допуска на окончательный размер служит чертеж. На предыдущие операции основанием служат экономический квалитет (см.3табл.3.1,с.150...151 или прил.9 метод. указаний) и соответствующий этому квалитету допуск размера. Для заполнения этой графы студент может использовать справочники, например / 22,табл. П 10/. /23,прил.П,с.335/,/б,табл.1.8,с.43/. Допуски размеров заготовок на отливок устанавливают по ГОСТ 1855-55*, ГОСТ2009-55* , допуски размеров заготовок из поковок и штамповок - по ГОСТ 7062-70*, ГОСТ 7505-55* и ГОСТ 7829-70*. Допуски размеров заготовок из проката устанавливаются па ГОСТ 2590-71* и ГОСТ 7417-57* и др. При отсутствии ГОСТов можно воспользоваться справочными данными. Приведенных в /3, 4, б, 96, II, 18/.
Графы 5 и 6. Наибольшие предельные размеры заготовки на данной операции определяются для вала путем сложения расчетного размера (графа 3) с соответствующим допуском (графа 4).
Для отверстия это будет расчетным размером (графа 3).
Наименьшие предельные размеры заготовки на данной операции для вала равны значению графы 3, а для отверстия это расчетный размерр (Графа 3) минус допуск (графа 4).
Графы 7 и 8. Наибольший припуск для вала устанавливается как разность между большими предельными размерами заготовки на предыдущей и последующей операциях.
Наибольший припуск для отверстия устанавливается как разность между наименьшими предельными размерами заготовки на данной и предыдущей операциях. Наименьший припуск для отверстия устанавливается как разность между наибольшими предельными размерами на данной и предыдущей операциях.
После выполнения всех расчетов студенту необходимо проверить правильность произведенных расчетов путем сопоставления разности припусков и допусков по формулам:
Zimax-Zimin=Ti-1-Ti;
2Zimax-2Zimin=Ti-1-Ti;
2Zomax-2Zomin=Ti-1-Ti;
Zomax-Zomin=Tз-Tд;
Значения припусков и допуски для этого вида заготовок регламентированы ГОСТ 7505-55. Припуски на обработку на сторону для штампованных заготовок приведены в табл. 20.
Выполнение сквозных отверстий или углублений в штамповках при изготовлении на молотах и прессах обязательно в тех случаях, когда оси отверстий или углублений совпадают с направлением движения бабы молота или ползуна пресса, а размеры и диаметры отверстий и углублений больше или равны высоте штампованных поковок.
Это положение распространяется на штамповки, у которых диаметры или размеры отверстий и углублений равны или больше 30 мм. В отдельных случаях рекомендуется применять впадины, не влияющие на стойкость штампов. Под высотой штампованной поковки подразумевается та высота, в которой находится отверстие.
Отклонения размеров для штампованных поковок приведены в табл. 21.
Таблица 20 Припуски на обработку для штампованных поковок второй группы (по ГОСТ 2789-51)
Примечание. Припуски даны на сторону в мм для шероховатости обрабатываемых поверхностей от v 1 до v3 класса чистоты.
При меньшей шероховатости поверхностной обработки к припускам: от V4 до v6 прибавляют 0,5 мм на сторону, от v 7 и выше 0,5-0,8 мм на сторону.
Таблица 21 Отклонения размеров на штампованные поковки второй группы (по ГОСТ 7505-55)
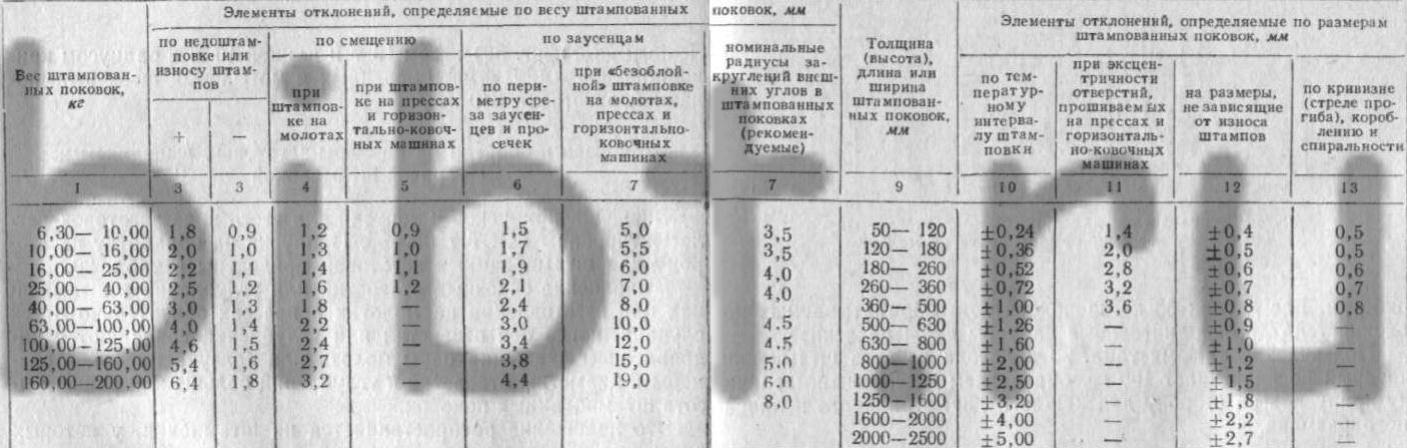
Примечание. Суммарные расчетные отклонения на размеры поковок округлять c точностью до 0,1 мм, причем если последний цифровой знак равен или более 5, то число округлять в большую сторону, если же последний цифровой знак менее 5, то в расчет не принимать.
Определение отклонений по толщине (высоте), длине и ширине штампованных поковок распространяется на все внешние размеры последних. Для внутренних размеров штампованных поковок следует применять этот же метод, но устанавливать отклонения с обратными знаками.
При изготовлении штампованных поковок на молотах и прессах на всех поверхностях деталей, располагающихся параллельно движению бабы молота или ползуна пресса, должны применяться штамповочные уклоны. В зависимости от применяемого оборудования, штамповочные уклоны соответствуют значениям, приведенным в табл. 22.
Таблица 22 Величина штамповочных уклонов
Для уяснения порядка определения номинальных размеров штамповок и допустимых отклонений рассмотрим следующий пример.
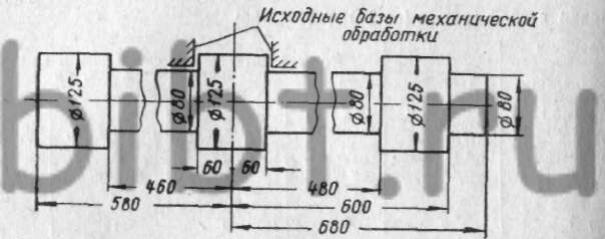
Фиг. 40. Эскиз детали для примерного расчета припусков и допусков горячей штамповки на молоте.
На фиг. 40 приведен эскиз вала для механической об>работки. Вес детали 63 кг, шероховатость обрабатываемых поверхностей v3, исполнительные размеры даны на эскизе.
Пользуясь данными табл. 20 и исходя из веса штамповки, который не превышает 100 кг,определяем поэлементно величину припусков на сторону для каждого диаметрального и линейного размера.
Для диаметра 80 мм припуск на сторону, мм 3,8
Для диаметра 125 мм припуск на сторону, мм 3,9
По длине на размер 60 мм припуск на сторону, мм 3,8
По длине на размер 460 мм припуск на сторону, мм 4,6
По длине на размер 480 мм припуск на сторону, мм.4,6
По длине на размер 580 мм припуск на сторону, мм 4,8
По длине на размер 600 мм припуск на сторону, мм 4,8
По длине на размер 680 мм припуск на сторону, мм 5,2
Округляя размеры поковок в большую сторону до 0,5 мм, будем иметь: диаметры 88 и 133 мм и линейные размеры с учетом припуска только на одну сторону (размер берется от оси) 84, 465, 485, 585, 605, 685 мм.
Штамповочные уклоны принимаем 5°+2 . Отклонение размеров принимаем по табл. 21.
Расчет производим следующим образом. По весу штамповки, руководствуясь графами 2 и 3, устанавливаем верхние и нижние отклонения. Затем, исходя из размеров штамповки, руководствуясь графой 10, устанавливаем допустимые отклонения, связанные с колебанием температуры. Так, для диаметра 133 мм при весе поковки до 100 кг по графам 2 и 3 имеем +4 мм и - 1,4 мм; по графе 10 ±0,36 мм. Суммируя эти величины и округляя результат, получаем +4,4 и 1,8 мм. Тогда оклонение для диаметра 133 +4,8 -1,8 и для диаметра 88 +4,2 -1,6 .
Для линейных размеров расчет ведется в том же порядке, при этом необходимо следить за тем, устанавливается допуск на размер, определяющий взаимное расположение двух поверхностей, или на размер, определяющий положение поверхности относительно оси. В первом случае к величинам, найденным по графам 2 и 3 прибавляются значения графы 10 с соответствующими знаками. Во втором случае значения, найденные по графам 2 и 3, берутся в половинном размере, так как положение оси принимается постоянным. К найденным величинам прибавляются значения графы 10 с соответствующими знаками.
Для размера 60 мм, проставленного от оси, принимаем половину величин, полученных по графам 2 и 3, соответственно +2 и - 0,7 мм; в графе 10 находим ±0,24. Округлив, получим 64 +2,2 -0,9 Размер 460 мм проставлен от оси, кроме того, этот размер является внутренним, поэтому значения отклонений по графам 2 и 3 следует принимать с обратными знаками. Итак, половина значений отклонений с обратными знаками -2 и +0,7 мм, по графе 10 ±1 мм. Округлив, получим 455 +1,7 -3. Соответственно для остальных размеров имеем 475+1,7 - 3 ; 585 +3,3 -2 605+3,3 -2 и 685+3,6 -2,2 .
Смещение по разъему штампа допускается 2,2 мм (графы 1 и 4). Заусенец по периметру среза 3 мм (графы 1 и 6). Радиусы округления внешних углов 4,5 мм.
С учетом найденных значний припусков и отклонений составляем чертеж штампованной поковки (фиг. 41).
Фиг. 41. Эскиз штампованной заготовки с припусками и допусками.
Существенное влияние на величину припуска кованых деталей и деталей из проката оказывает термообработка. Если деталь после ковки проходит черновую механическую обработку, затем термообработку и чистовую механическую обработку, то в этом случае должен быть предусмотрен припуск, который компенсирует погрешности, возникающие при термообработке. Такой порядок обработки связан с тем, что при наличии крупных заготовок мы не можем обеспечить необходимую структуру и механические свойства по всему сечению, либо твердость в результате термообработки возрастает настолько, что осложняет, снятие припусков на обдирочных операциях.
Если же деталь в состоянии заготовки проходит термообработку, предусмотренную техническими условиями, то в этом случае отпадает необходимость увеличения припуска перед чистовой механической обработкой. Таким образом, проведение термообработки в состоянии заготовки обеспечивает снижение припуска, сокращение цикла производства и затрат труда. Так, например, при изготовлении вала диаметром 160 мм, длиной 4600 мм с термообработкой в состоянии заготовки, вместо обдирки и последующей термообработки, мы имеем следующие результаты:
а) уменьшение припусков и сокращение за счет этого расхода металла на 190 кг, или на 17%;
б) сокращение затрат времени на механическую обработку на 20%;
в) сокращение производственного цикла на б суток, или на 32%.
В зависимости от марки материала и вида термообработки, установлены значения сечений, при которых возможно проведение термообработки в состоянии заготовки, (табл. 23).
Таблица 23 Сечение деталей, проходящих термообработку в заготовке, в зависимости от марки материала и вида термообработки
Чертеж исходной заготовки отличается от чертежа готовой детали прежде всего тем, что на всех обрабатываемых поверхностях предусматриваются припуски, соответственно изменяющие размеры, а иногда и форму заготовок. Форма отдельных поверхностей исходных заготовок определяется с учетом технологии получения заготовок, требующей в ряде случаев определенных уклонов, радиусов закругления и т. п.
Общим припуском на обработку называется слой материала, удаляемый с поверхности исходной заготовки в процессе механической обработки с целью получения готовой детали.
Установление правильных размеров припусков на обработку является ответственной технико-экономической задачей. Назначение чрезмерно больших припусков приводит к непроизводительным потерям материала, превращаемого в стружку; к увеличению трудоемкости механической обработки; к повышению расхода режущего инструмента и электрической энергии; к увеличению потребности в оборудовании и рабочей силе. При этом затрудняется построение операций на настроенных станках, снижается точность обработки в связи с увеличением упругих отжатий в технологической системе и усложняется применение приспособлений.
Назначение недостаточно больших припусков не обеспечивает удаления дефектных слоев материала и достижения требуемой точности и шероховатости обрабатываемых поверхностей, а также вызывает повышение требований к точности исходных заготовок и приводит к их удорожанию, затрудняет разметку и выверку положения заготовок на станках при обработке по методу пробных ходов и увеличивает опасность появления брака.
Операционный припуск - это слой материала, удаляемый с заготовки при выполнении одной технологической операции (ГОСТ 3.1109-82). Операционный припуск равняется сумме промежуточных припусков, т. е. припусков на отдельные переходы, входящие в данную операцию.
Операционный допуск должен быть достаточно широким, чтобы облегчить выполнение данной операции, и не слишком широким, чтобы не вызывать чрезмерного увеличения припуска для последующей операции и соответствующего ее удорожания.
Изложенный расчетно-аналитический метод определения припусков и промежуточных размеров применяется при проектировании исходных заготовок и отдельных операций технологического процесса крупносерийного и массового производства, а также процессов обработки крупных и особенно ответственных деталей серийного и даже единичного производства.
В условиях единичного и серийного производств обычных деталей средней точности для определения общих и операционных припусков часто пользуются нормативными таблицами припусков, разработанными различными авторами на основе изучения обширного практического опыта промышленности и рекомендуемыми для некоторых средних условий производства. Пользование подобными таблицами ускоряет процесс проектирования и является во многих случаях допустимым, однако при этом необходим анализ соответствия конкретных условий проектируемого процесса условиям, для которых были составлены нормативные таблицы. Во всех случаях отклонений условий проектируемого процесса от стандартных, для которых составлены таблицы, необходимо уточнять рекомендуемые припуски соответствующим расчетом. Так, например, при шлифовании длинных и тонких планок после их закалки, вызывающей коробление заготовок, невозможно ограничиваться установлением припуска на шлифование по табличным данным, а следует дополнительно определить расчетным или экспериментальным путем ожидаемую величину, связанную с прогибом заготовок при закалке. Затем следует убедиться, что установленный по таблицам припуск на шлифование достаточен для компенсации коробления и при необходимости соответственно увеличить припуск.
При пользовании нормативными таблицами припусков следует также учитывать, что они дают значения номинальных, а не минимальных припусков и включают в себя значения допусков предшествующих операций. В связи с этим при изменении точности предшествующей обработки должна измениться и величина табличного припуска.
Промежуточные припуски имеют важное значение в процессе разработки технологических операций механической обработки детали. Правильное назначение промежуточных припусков на обработку заготовки обеспечивает экономию материальных и трудовых ресурсов, качество выпускаемой продукции, снижает себестоимость изделий и ускоряет дальнейшее развитие машиностроительной промышленности и всего народного хозяйства страны.
В массовом и крупносерийном производстве промежуточные припуски рекомендуется рассчитывать аналитическим методом, что позволяет обеспечить экономию материала, электроэнергии и других материальных и трудовых ресурсы производства.
В серийном и единичном производствах используют статистический (табличный) метод определения промежуточных припусков на обработку заготовки, что обеспечивает более быструю подготовку производства по выпуску планируемой продукции и освобождает инженерно-технических работников от трудоемкой работы.
После расчета промежуточных размеров определяют допуски на эти размеры, соответствующие экономической точности данной операции. Промежуточные размеры и допуски на них определяют для каждой обрабатываемой поверхности детали.
Черновые операции обычно следует выполнять с более низкими техническими требованиями на изготовление (12-14 квалитет), получистовые – на один-два квалитета ниже и окончательные операции выполняются по требованиям рабочего чертежа детали.
Шероховатость обрабатываемых поверхностей зависит от степени точности и назначается по справочным таблицам.
Необоснованное повышение качества поверхности и степени точности обработки повышает себестоимость изготовления детали на данной технологической операции.
При назначении промежуточных предельных отклонений необходимо учитывать данные рекомендации при разработке технологического процесса изготовления деталей.